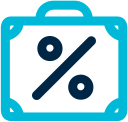
Personal system of discountsfor wholesale buyers
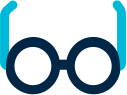
Consultation technologistselection of the dispersion and the adhesive, the implementation in the production
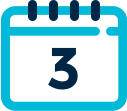
Term of execution of the order from 3 daysround-the-clock production
UMACOLL 834M
Technical conditions: ТУ 2252-034-20514586-15
- Container:
- 30 kg (plastic bucket)
Description
Umacoll 834M is a two-packed glue based on polyurethane dispersion and polyisocyanate hardener. Protect from freezing!
Usage
DESCRIPTION
Umacoll 834M is used for wood-based textured boards (HDF, chipboards, laminated chipboards, MDF, etc) 3D-lamination and thermo veneer with thermoplastic films (PVC, PET, ABS) in diaphragm and vacuum pressing.
FIELDS OF APPLICATION
Umacoll 834M is used for wood-based textured boards (HDF, chipboards, laminated chipboards, MDF, etc) 3D-lamination and thermo veneer with thermoplastic films (PVC, PET, ABS) in diaphragm and vacuum pressing.
SUBSTRATE
Easy to spray. Suitable viscosity application. Finished adhesive bond has a high initial strength, moisture and steam resistance, frost resistance up to-40 ° C and thermal resistance up to +110 ° C.
Technical information
Umacoll 834M | Umacoll 04 | |
Base | Polyurethane dispersion | Polyisocyanate |
Form | White, dry transparent | Transparent, colourless to yellowish |
Viscosity Brookfield LVT, mPа*s | 1000-4000*(23/63/12) | - |
Density, g/cm3 | 1,040±0,02 | ~1,16 |
рН value | 7,5±0,5 | - |
Reactivation time | 24 hours | |
Activation temperature **, оС | 55-65 | |
Bond thermal stability , оС (Covestro method) | No less 110 |
* More definite viscosity is available to customers need.
** Pressing bond temperature providing 100% adhesive reactivation.
Manufacture determined technical data can vary depending on the storage conditions (within the standard).
Application
CONDITIONS
Working temperature +15 °С, optimum temperature (20±2)о С and air humidity no more than 65%. Gluing materials and glue should be withstood to the room temperature before use.
Preparing |
Umacoll 834M should be mixed thoroughly with Umacoll 04 hardener to homogeneous mixture. Mixing time is about 2 min. Two component system use: stir thoroughly 100 weight fr. of. Umacoll 834M and 5 weight fr. of Umacoll 04. Replacing Umacoll 04 hardener with another is not allowed! Stir thoroughly before use and filter to delete films and flocculated polymer to prevent spraying nozzle loading/ |
Pot life |
Mixture pot life is about 8 hours depending on the air temperature. |
Tools |
Spray gun. Optimum nozzle diameter 1,2-2,0 mm, spraying pressure 2,4-4 bar. (Nozzle diameter and pressure data are obtained using DeviBiss PRI PRO 210-14k. Pressure is set at injection tube output). Nozzle diameter and optimum pressure should be defined in each case individually. Glue contact materials should be corrosive resistant. No contact with copper, aluminium and zinc (glue coagulation is possible. |
Cleaning |
Equipment is washed with water before glue drying. Dry glue is cleaned mechanically. Use dry tools for refilling. |
Application |
Spray gun on glued materials bearing side. Glue consumption is about 50 g/m2. Milled rounded 3D - surface areas (surfaces with high absorbency) should be retreated with glue second layer after first layer complete drying. Optimum technological parameters should be set regarding manufacturing conditions and materials used.
|
Adhesive |
Bonding layer must be dried at room temperature before pressing. First layer drying is 30 min, second layer drying is 60 min. To fasten drying time use heat increasing drying temperature up to 30-350 C. Bonding is achieved by adhesive line thermo activation.
Pressing condition:
Optimum technological parameters should be set regarding manufacturing conditions and materials used. Glued parts can be machined after 6 hours. Full time of hardening is 3-7 daysю |
Storage
STORAGE
Glue components should be kept in tightly closed original container in dry rooms, not below +5° up to +30°С. Protect from freezing!
GUARANTED STORAGE LIFE
Umacoll 834M, Umacoll 04 expire date is 6 months in case if delivery and storing rules are followed. After expire date shouldn’t be used without tests.
HEALTH AND SAFETY
Careful air change is necessary. Avoid skin or eye contact. Use rubber gloves to protect hands. Respiratory protection is required when spraying. Keep away of children. For detaled safety instructions, please read safety certificate.
RECYCLING
Packing materials are recycled as consumer waste.