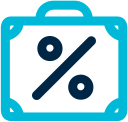
Personal system of discountsfor wholesale buyers
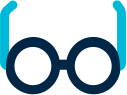
Consultation technologistselection of the dispersion and the adhesive, the implementation in the production
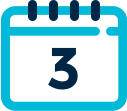
Term of execution of the order from 3 daysround-the-clock production
UMACOLL 85M
Technical conditions: 2252-034-20514586-15
- Container:
- 30 kg (plastic bucket)
Description
One component water-based polyurethane-dispersed adhesive with technological additives for 3-D lamination.The adhesive has an increased thermal resistance with a sufficiently long reactivation time.
The product should be protected from freezing!
Usage
Application area
Umacoll 85M is designed for 3D-gluing and heat-setting of relief panels of wood materials (fiberboard, chipboard, chipboard, MDF, etc.) with thermoplastic furniture films (PVC, PET and ABS) in membrane and vacuum presses.
Specificity of application
The adhesive has a good spraying ability, convenient for applying viscosity. The resulting adhesive seam in the finished product has a high initial strength, resistance to moisture and steam, frost resistance up to -40°C and heat resistance not less than + 90°C.
Technical information
The basis |
Polyurethane dispersion |
Colour |
In agreement with the consumer is produced in 2 modifications:
|
Viscosity according to Brookfield LVT, mPa * s |
1000-4000* (23/63/12) |
Density, g / cm3 |
1,040±0,02 |
PH value |
7,5±0,5 |
Reactivation time |
24 hours |
Activation temperature **, ° C |
55-65 |
Temperature resistance of the adhesive joint, ° С |
not less than 90 |
* - As agreed with the customer, the adhesive can be manufactured with a viscosity in a narrow range. ** - The temperature of the adhesive joint during pressing, which ensures 100% reactivation of the adhesive. Technical characteristics, determined at the time of product manufacture, depending on storage conditions may vary (within the limits of the norm). |
Application
Surface preparation
The surface of the materials to be bonded must be dust-free, should not have obvious fat and other impurities.
Application conditions
Operating temperature - from + 15°C, optimum temperature (20 ± 2)°С, air humidity - not more than 65%. Adhesives and materials must be acclimatized to room temperature before recycling.
Application process
Preparation |
Before use, the adhesive should be thoroughly mixed and strained through a polymer mesh to remove the film and the coagulated polymer to prevent the nozzle from clogging during spraying. Umacoll 85M is fully ready for use. |
Viability |
The viability of Umacoll 85M is not limited during the warranty period of storage. |
Instruments |
Spray gun. The optimum diameter of the nozzle is 1.2-2.0 mm, the spray pressure is 2.4-4 bar. (Data on the diameter of the nozzle and pressure are obtained using DeviBiss PRI PRO 210-14k .The pressure is set at the outlet of the discharge pipe). In each particular case, the optimum pressure and nozzle diameter must be selected individually. Materials contacting with the adhesive must be corrosion-resistant. Avoid contact with copper, aluminum, zinc (may lead to coagulation of the adhesive). |
Washing |
Equipment and tools after use, rinse with water, avoiding the drying of the glue. In case of glue drying, the tool should be cleaned of the hardened adhesive residues mechanically. Before refilling, tools must be dry. |
Application |
It is produced by a spray gun on the supporting side of the materials to be glued. The adhesive consumption is about 50 g / m2 per plate. On milled rounded 3D areas of the surface (surfaces with high absorbency), a second layer of glue should be applied after the first layer has completely dried. Optimum technological parameters should be established in relation to the conditions of the specific production and materials used. |
Gluing |
Before pressing, the adhesive layer must be dried at room temperature. The drying time of one layer is 30 minutes, the 2nd layer 60 minutes. The drying process can be accelerated by supplying heat, raising the drying temperature to 30-35 ° C Bonding is carried out by thermal activation of the adhesive seam. Pressing parameters:
Optimum technological parameters should be established in relation to the conditions of the specific production and materials used.
Before further processing, the parts must be kept for at least 6 hours. Full hardening of the adhesive seam occurs in 3-7 days. |
Storage
Storage conditions
Store in tightly closed containers of the manufacturer in dry rooms at temperatures from +5 to + 30°C. Do not freeze!
Warranty period of storage
The warranty period for Umacoll 85M is 6 months from the date of manufacture, provided that the consumer observes the rules of transportation and storage. After the expiration of the storage warranty period, it is not recommended to use the product without laboratory testing.
Precautionary measures
During the work, it is necessary to thoroughly ventilate the room. Avoid contact with skin and eyes. Use rubber gloves to protect hands. After contact with skin, wash with plenty of water. In case of contact with eyes, rinse immediately with plenty of water and seek medical advice. Keep out of the reach of children. During spraying required respiratory protection. For complete information, see the safety data sheet for the product.
Recycling
Tare from the glue to be disposed of as household waste.